Setting up a 75mm HDPE Mono Film Plant with a Beam Winder involves several stages, from the installation of equipment to adjusting settings for optimal performance. Here’s a comprehensive guide to help you through the entire process:
1. Pre-Installation Requirements
Before setting up the plant, ensure you have the following:
- Location: A clean and spacious area with proper ventilation.
- Power Supply: Stable 3-phase power supply (usually 400V).
- Water Supply: Adequate cooling water for the extruder.
- Compressed Air: Required for some pneumatic components.
- Materials: HDPE granules (with specific melt flow index, density, and additive compatibility).
- Team: Skilled operators, technicians, and engineers.
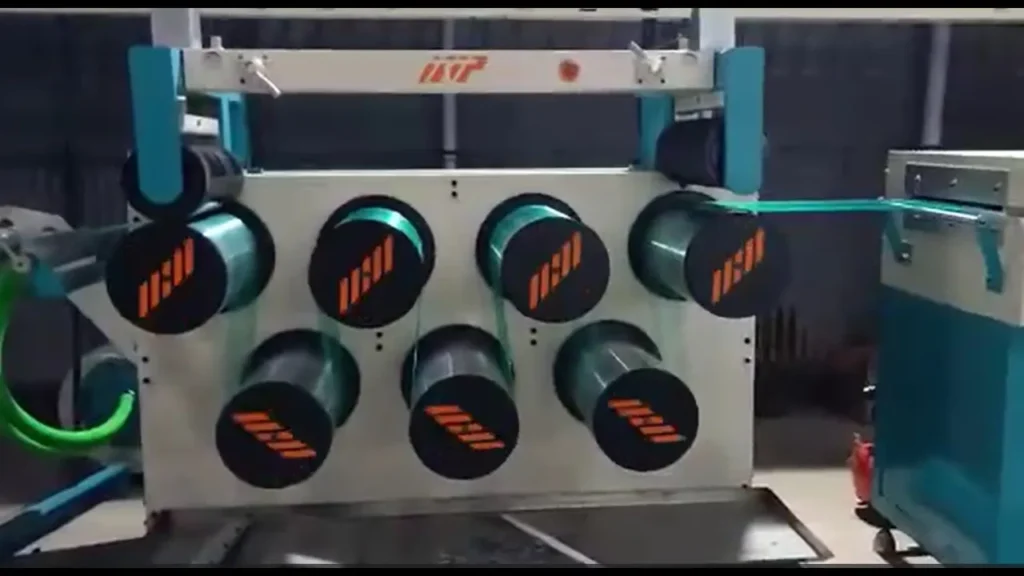
2. Equipment Required
- HDPE Mono Film Plant: The core of the plant, used for melting and extruding HDPE resin into film.
- Features: Hopper, barrel, screw (with heating zones), die head.
- Chill Roll Unit: Cools and solidifies the extruded film.
- Features: Steel or rubber-coated rollers, water cooling system.
- Corona Treater: Enhances the surface energy of the film to improve printability and adhesion.
- Beam Winder: Collects the film on large rolls after processing.
- Features: Tension control, speed adjustment, and beam size accommodation.
- Trim Winder/Edge Trimmer: Removes excess material from the edges.
- Control Panel: Centralized system for monitoring and controlling extruder temperature, speed, and winder operations.
- Auxiliary Equipment: Cooling tower, vacuum pumps, conveyors. HDPE Mono Film Plant
3. Installation Process
a) Positioning the Extruder
- Ensure that the extruder is placed on a level surface.
- Align the machine to minimize vibrations during operation.
- Connect the power supply and ensure all electrical connections are secured.
- Attach the cooling system (chill rolls, vacuum systems, and water supply).
b) Mounting the Die Head
- Attach the die head to the extruder outlet, ensuring it’s tightly secured.
- Adjust the gap between the die lips to control film thickness.
c) Chill Roll Setup
- Position the chill roll unit directly after the die head.
- Ensure the rollers are parallel to avoid wrinkling of the film.
- Connect water supply for the cooling system.
d) Corona Treater Assembly
e) Beam Winder Installation
- Set up the beam winder at the final stage of the film process.
- Ensure the tension and winding speed are adjustable.
- Load an empty beam core onto the winder and secure it in place. HDPE Mono Film Plant
4. Calibration and Settings
a) Extruder Settings
- Temperature Zones: Set appropriate temperatures for the extruder, typically ranging between 180°C and 230°C depending on the HDPE grade.
- Screw Speed: Set the screw rotation speed to control the extrusion rate.
b) Die Head Settings
- Adjust the die lips to control the film’s thickness, typically ranging from 20 microns to 100 microns.
c) Chill Roll and Cooling
- Adjust the chill roll speed to synchronize with the extrusion speed.
- Ensure the cooling water is flowing at the correct rate to solidify the film uniformly.
e) Beam Winding
- Set the winding tension to avoid film stretching or sagging.
- Adjust the winding speed in sync with the extruder and chill rolls.
5. Trial Run
a) Start the Extruder
- Feed HDPE granules into the hopper. HDPE Mono Film Plant
- Gradually increase the temperature of the zones and start the screw rotation.
b) Film Extrusion
- Once the HDPE is fully melted, film will begin to extrude from the die head.
- Guide the film onto the chill rolls, ensuring it cools uniformly.
c) Corona Treatment and Winding
- After the film passes through the chill rolls, guide it through the corona treater.
- From the corona treater, lead the film to the beam winder. HDPE Mono Film Plant
6. Fine-Tuning and Adjustments
- Thickness Control: Adjust the die lips or screw speed to get the desired film thickness.
- Winding Tension: Ensure the beam winder is not overstretching the film by fine-tuning the tension control.
- Cooling Efficiency: Monitor the cooling system to ensure the film is adequately solidified before it reaches the winder.
7. Maintenance Tips
- Regularly clean the die head to avoid buildup of material.
- Inspect the chill rolls for any wear or contamination that could affect the film quality.
- Lubricate moving parts (like the beam winder and extruder screw) as per the manufacturer’s instructions.
- Regularly check the electrical connections and ensure all components are functioning properly.
8. Safety Precautions
- Ensure operators are trained in handling hot surfaces and machinery.
- Use appropriate personal protective equipment (PPE), such as gloves and eye protection.
- Have emergency power shut-off systems in place.
This guide covers the key steps for setting up a 75mm HDPE Mono Plant with a Beam Winder. Fine-tuning the process based on your plant’s specific requirements and material grade is essential to achieving high-quality film production.
Full Setup Guide for 75mm HDPE Mono Film Plant
HDPE Mono Film Plant, HDPE Mono Film Plant, HDPE Mono Film Plant